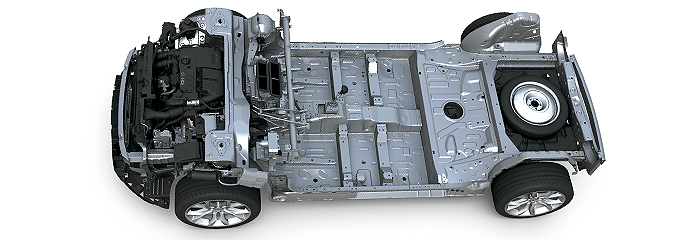
Revolución en las fábricas
- Plataformas comunes: menor coste, peso, consumo, emisiones y más equipamiento para los modelos más modestos.
10 diciembre 2015
¿Alguna vez se han preguntado que comparten un Nissan “X-Trail” y el nuevo Renault “Mégane”? ¿O el Audi “A3” y el Skoda “Octavia”? Solución: las plataformas; es decir, la estructura inferior del vehículo. La utilización por parte de los fabricantes de plataformas o arquitecturas comunes a varios modelos está suponiendo, desde hace años, una revolución clave en el sector. Se trata de un cambio ‘de calado’ en la fabricación de coches que, en muchos casos, permite ahorrar miles de millones de euros, y dar un giro de 180 grados a la flexibilidad en la producción, puesto que, de una misma línea de montaje, pueden salir al mismo tiempo una berlina, un compacto, un todocamino o un utilitario, por poner algunos ejemplos, reduciendo el número de piezas utilizadas, el tiempo empleado o el dinero invertido.
Aunque la Alianza Renault Nissan no fue la primera que recurrió a esta solución con el objetivo de ahorrar costes, sí ha sido uno de los grupos que más flexibilidad ha otorgado a su sistema de módulos, que, sobre una base mecánica muy flexible, permite fabricar una gran variedad de modelos diferentes. Y es que además del “Qashqai” y el “Kadjar”, sobre la plataforma CMF (Common Module Family) de dicha alianza también se asientan modelos tan dispares como un Renault “Espace”, Nissan “X-Trail”, el nuevo “Mégane” o Renault “Talismán”, entre otros.
Mayor competitividad
Hasta no hace mucho, lo normal era que cada segmento partiese de una plataforma individualizada con unas medidas, utilización de aceros e incluso esquema de suspensiones específicas que obligan al fabricante a un despliegue de medios desproporcionado y a dedicar una línea de producción casi para cada modelo, una inversión que se tardaba muchísimo tiempo en amortizar. Pero la crisis, la globalización y la incesante búsqueda de la optimización de los recursos han propiciado una estrategia que ya está dando frutos. Y el resultado ha sido clave para muchos. Mayor competitividad, economía de escala, mayor flexibilidad en la producción, sinergias, industrialización más barata...
En el caso de Renault, las cifras despejan cualquier duda: la marca francesa se ahorra entre un 30 y un 40% de ingeniería de desarrollo o un 20% en compra de componentes. De hecho, buena parte de los 3.800 millones de euros de reducción y ahorro de costes que la Alizanza Renault-Nissan ha registrado en 2014 corresponden al ahorro generado por la nueva arquitectura. La Alianza espera que, de aquí a 2020, un 70% de sus vehículos construyan sobre arquitecturas CMF.
Objetivo: ahorrar
Pero esto no es solo una práctia de Renault y Nissan. El grupo VAG -que comprende Volkswagen, Audi, Seat, Skoda y hasta doce marcas- inició hace ya ocho años la política de plataformas compartidas con modelos como el "A4", "A5", "A6"... compartiendo una base denominada MLB. Aunque realmente fue en 2012, con la llamada MQB, cuando comenzó a ahorrar dinero de verdad multiplicando el número de vehículos que aprovechan esta plataforma, y la idea de este grupo es que la lista de modelos con la misma estructura aumente hasta treinta.
Menos consumo y emisiones
Al margen de lo que un fabricante ahorra compartiendo plataformas, hay que destacar también las ventajas que repercuten en los vehículos que se producen mediante esa nueva estrategia. La más importante es la reducción de peso, un punto clave que beneficia al consumo y emisiones y permite añadir mayor equipamiento. También se reduce el centro de gravedad del vehículo, lo que permite mejorar el comportamiento y poner menos trabas a un diseño más aerodinámico.
Se podría definir como el conjunto de elementos de la estructura inferior del automóvil del que forman parte las suspensiones y la dirección. Es la base de cada vehículo y sobre la que se va a colocar la carrocería, los asientos, el motor…